L’ETH Zurich explore une nouvelle méthode de fabrication pour un escalier en béton

Des approches de construction économes en matériaux et réversibles sont présentées dans l’escalier en colimaçon en béton Cadenza, créé par des chercheurs de l’université technologique ETH Zurich en collaboration avec ROK Architects.
L’escalier Cadenza est la dernière contribution au bâtiment NEST, un laboratoire de techniques de fabrication expérimentales qui ETH Zurich partage avec d’autres instituts de recherche de la ville suisse de Dübendorf.
L’escalier Cadenza a été installé entre les étages de la dernière unité du bâtiment, appelée STEP2, et comporte 16 marches en béton préfabriquées identiques disposées en forme hélicoïdale.
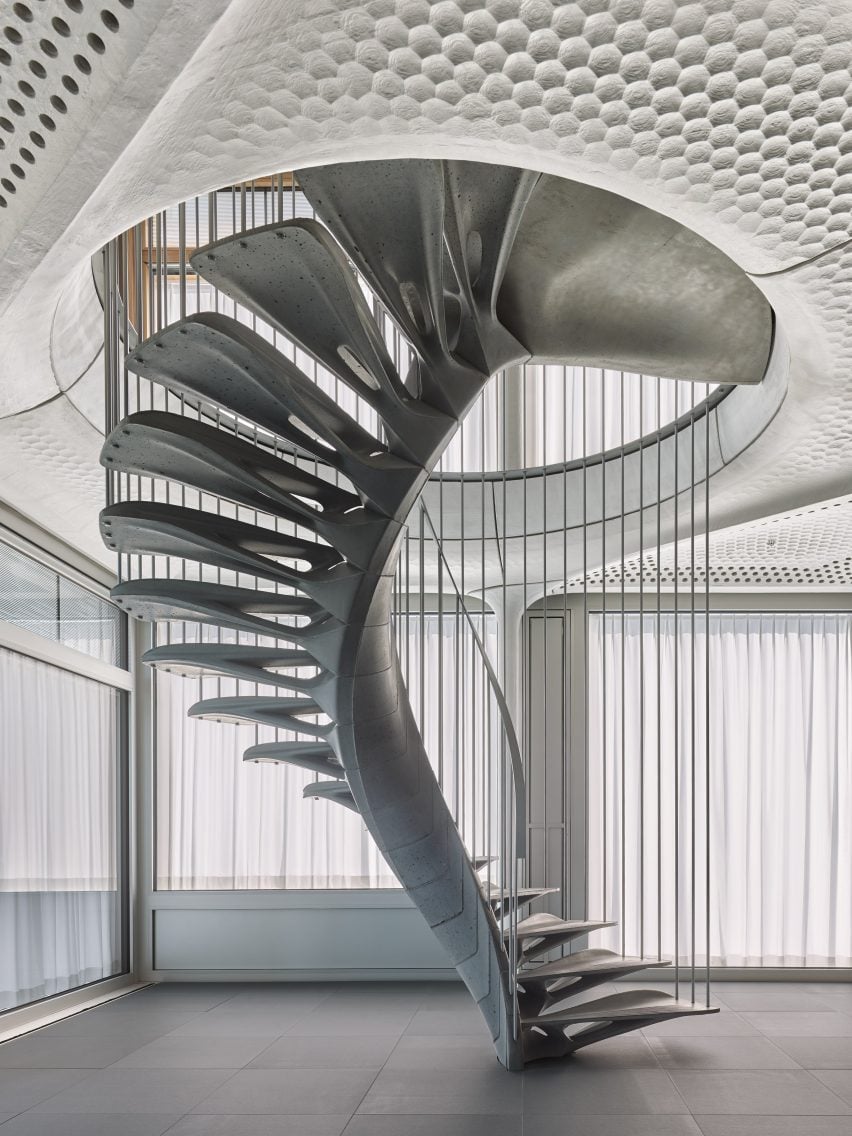
Les marches ont toutes été réalisées à partir du même moule imprimé en 3D, répondant à la problématique des déchets liés aux coffrages à usage unique couramment utilisés pour le béton, et sont maintenues en place par des liaisons sèches.
Cela signifie qu’ils peuvent être démontés et réutilisés dans un autre bâtiment au lieu d’être démolis.
La quantité de béton utilisée a également été réduite au minimum requis, ce qui ajoute à l’esthétique inhabituelle de l’escalier, composée de formes élancées et squelettiques.
Technologies numériques du bâtiment de l’ETH Zurich Le directeur Benjamin Dillenburger a déclaré que l’escalier symbolisait les avantages des outils numériques dans l’architecture et l’ingénierie et que la solution était prête à être utilisée dans des projets de construction individuels.
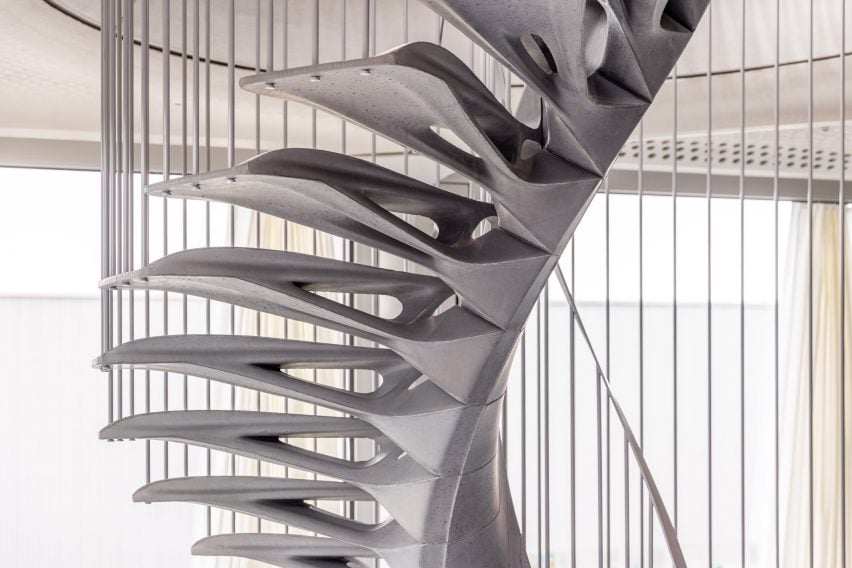
« Les structures en béton personnalisées constituent un défi pour les coffrages conventionnels », a déclaré Dillenburger. « Les cadres numériques de la conception à la production avec coffrages imprimés en 3D offrent d’énormes avantages en termes d’expression architecturale, de performances structurelles et d’efficacité des matériaux. »
« Les marches ont une épaisseur de seulement 20 millimètres et ont été structurellement optimisées pour une réduction drastique du poids », a-t-il poursuivi. « Leur production entraîne peu de déchets puisqu’un seul jeu de coffrages imprimés en 3D permet de réaliser toutes les étapes. »
Les moules des marches sont imprimés en 3D à partir de plastique PET renforcé de fibres de carbone. Alors que certains ingénieurs pourraient être tentés d’imprimer en 3D les escaliers directement en béton, les chercheurs du projet voient plutôt un avantage à imprimer le coffrage.
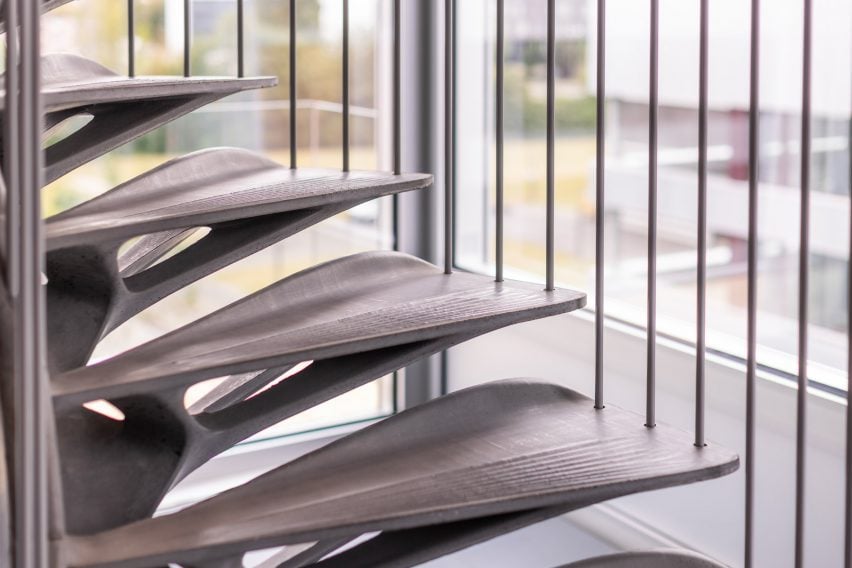
« Un ensemble compact et réutilisable de coffrages imprimés en 3D peut être utilisé pour couler plusieurs étapes à plusieurs reprises », a déclaré à Dezeen l’assistante de recherche Angela Yoo.
« Cela permet d’assembler plusieurs volées d’escaliers avec un minimum de fabrication numérique, ce qui en fait une solution idéale pour la production évolutive de conceptions sur mesure. »
Cette approche permet également l’intégration de renforts en acier, a-t-elle ajouté, ce qui est généralement incompatible avec l’impression 3D car les barres gênent la fabrication.
L’escalier Cadenza a été assemblé hors site et descendu dans le bâtiment NEST par grue, bien que l’ETH Zurich affirme qu’il peut être manipulé et assemblé sans machinerie lourde et être installé dans des espaces restreints, y compris lors de rénovations.
Les différentes marches sont constituées de béton renforcé de fibres d’acier à très haute résistance et pèsent 45 kilogrammes, soit environ 60 pour cent de moins qu’une marche en béton conventionnelle. Différentes conceptions sont possibles en utilisant le même flux de travail informatique, développé avec la société suisse Architectes de la République de Corée.
L’assemblage est facilité par deux composants : le premier est une série de connecteurs imbriqués imprimés dans chaque marche pour se fixer les uns aux autres avec précision, et le second est un système de trois câbles en alliage d’acier qui passent à travers des canaux dans les marches le long de la colonne vertébrale du escalier.
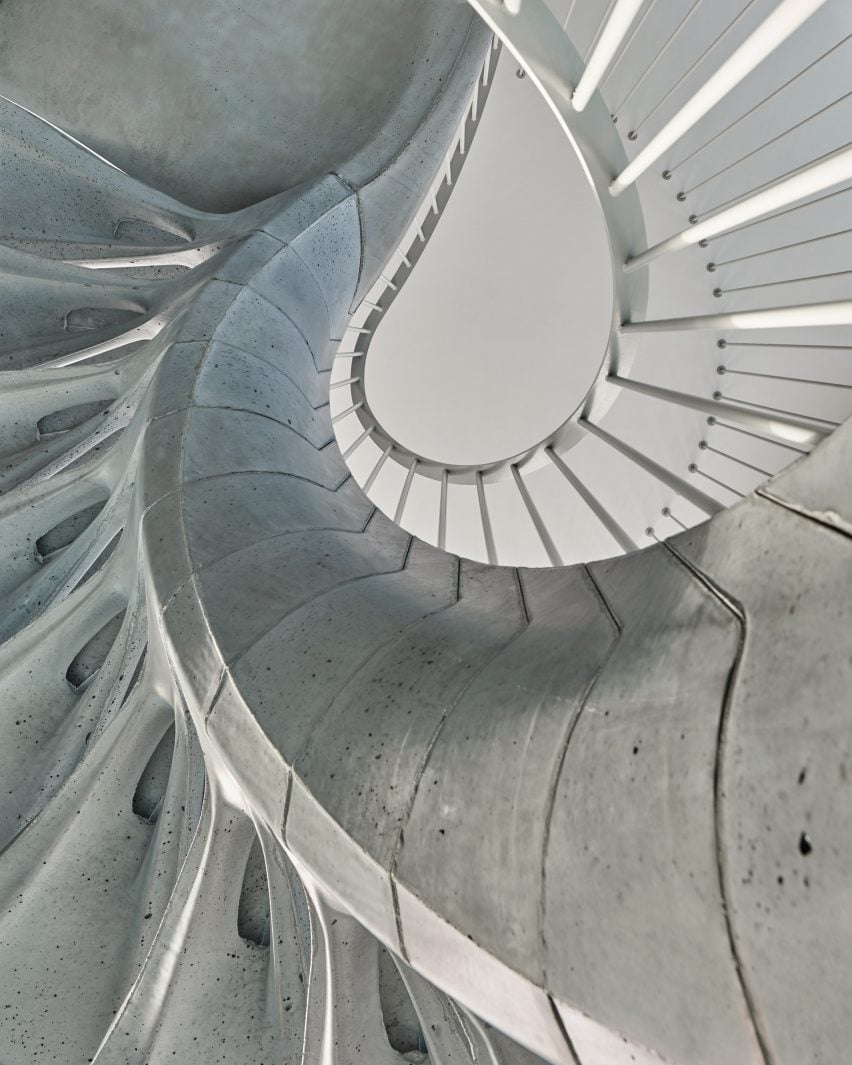
Il s’agit d’un système de post-tension, la tension n’est donc appliquée sur ces barres qu’une fois les marches en place, grâce à une brève application de chaleur via un générateur. Cela a pour effet de maintenir les marches bien serrées au centre de l’escalier.
« La précontrainte est basée sur ce que l’on appelle ‘l’acier à mémoire’, qui peut développer de fortes forces par chauffage et refroidissement », a déclaré Michael Knauss, co-fondateur de ROK. « Par rapport aux méthodes conventionnelles, ce système permet d’économiser de l’espace et est facile à utiliser. »
Le système de tension peut être démonté et les marches individuelles peuvent être démontées, ce qui en fait une technique de construction circulaire, tandis que le béton lui-même devrait avoir une longue durée de vie qui, selon certains, compense ses émissions élevées de carbone.
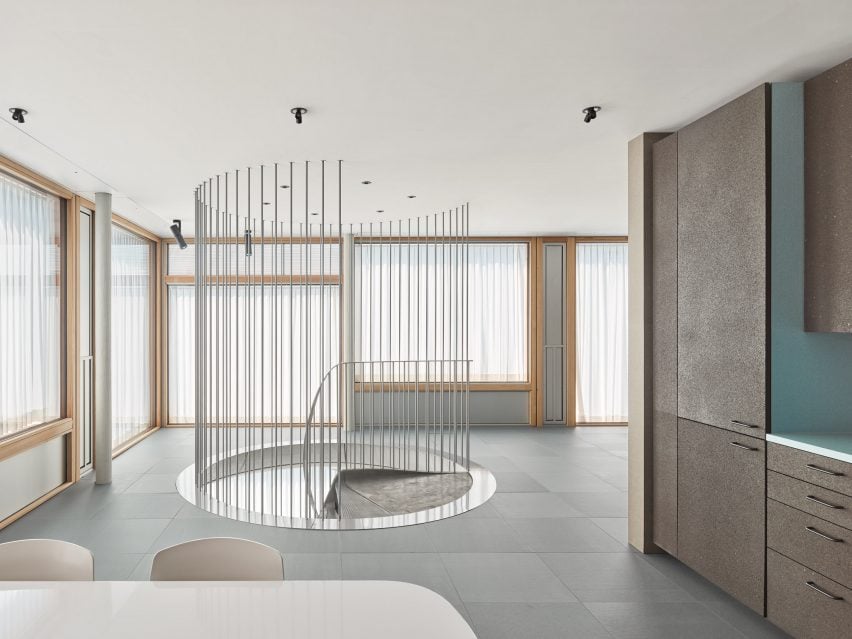
« À bien des égards, les éléments préfabriqués en béton contribuent à la durabilité dans la construction », a déclaré Klaus Einfalt, PDG du partenaire de fabrication SW Umwelttechnik. « Leur stabilité, leur longévité et leur recyclabilité en font un facteur essentiel pour un avenir durable dans le secteur de la construction. »
Le bâtiment NEST est dirigé par les instituts de recherche suisses Empa et Eawag et a été inauguré en 2016. Il se compose de trois plates-formes ouvertes sur lesquelles différents modules comme l’unité STEP2 peuvent être installés pendant une durée limitée, avant d’être démontés une fois la recherche terminée.
Les travaux antérieurs entrepris dans l’installation comprenaient le plafond en dalles de béton HiRes avec des conduits de ventilation imprimés en 3D et une méthode de construction robotisée pour les structures en bois.